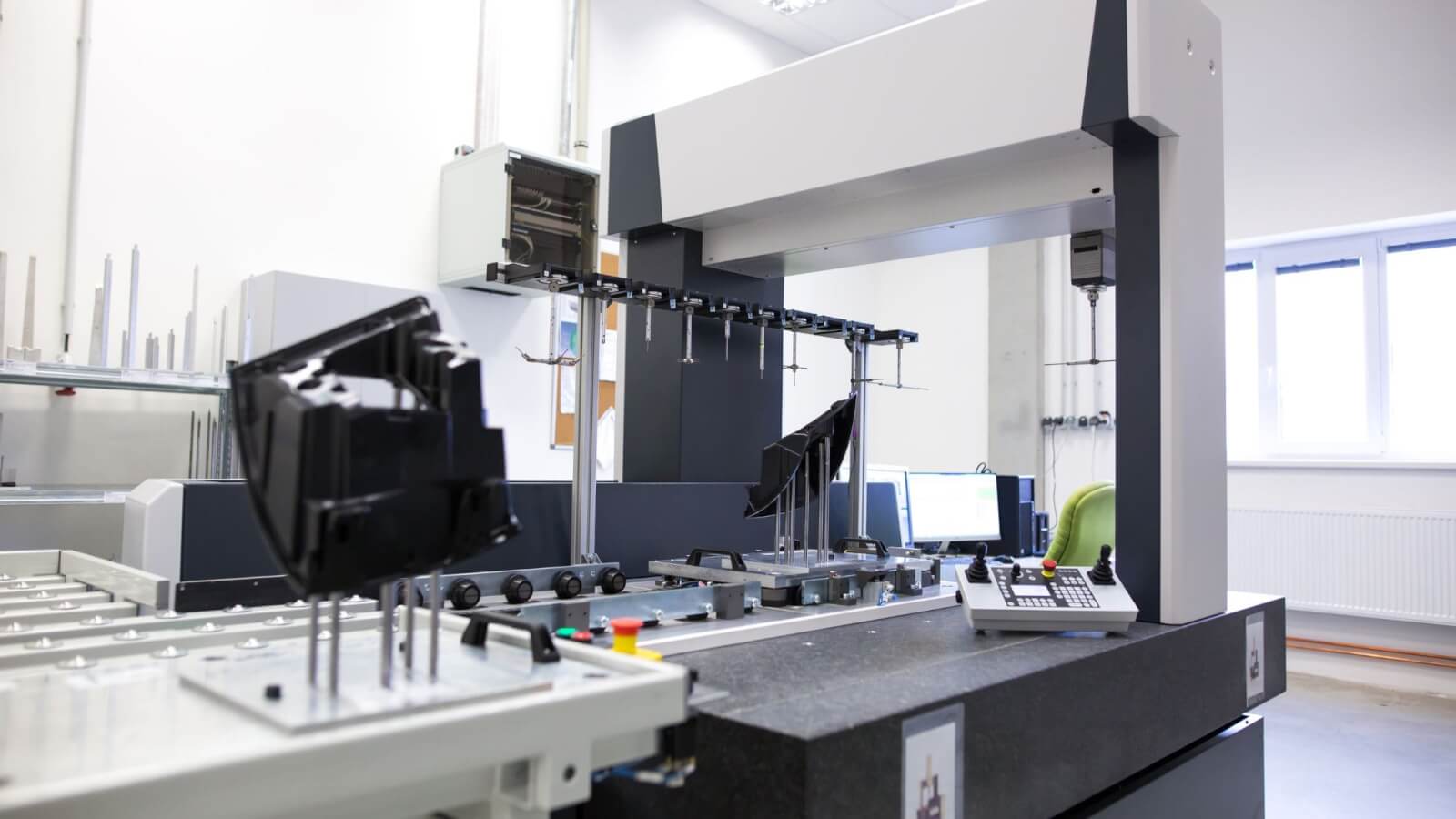
Plastic injection molding – the very heartbeat of modern manufacturing. Imagine taking a simple idea and transforming it into a tangible reality, all thanks to this revolutionary process. Join us on a journey through the fascinating world of plastic injection molding, where innovation meets creativity to shape our everyday lives in ways we never thought possible.
The Process of Plastic Injection Molding
In the intricate dance of plastic injection molding, precision and efficiency reign supreme. It all starts with the design phase, where engineers meticulously craft the blueprint for the mold that will bring our vision to life. Next comes the selection of raw materials – carefully chosen based on their properties and intended application.
Once everything is in place, it’s time for the main act: injection molding itself. The process begins as molten plastic is injected into a mold cavity at high pressure, filling every nook and cranny with liquid potential. Cooling follows swiftly, solidifying the material into its final form.
After cooling complete, it’s like unwrapping a gift as the newly formed part is ejected from the mold. What was once just an idea now stands before us – a tangible creation born from innovation and technology intertwined seamlessly in this remarkable manufacturing process.
Applications of Plastic Injection Molding
Plastic injection molding is a versatile manufacturing process that finds applications in various industries. From automotive parts to medical devices, plastic injection molding plays a crucial role in bringing innovative designs to life.
In the automotive industry, Plastic Injection Molding is used to create interior and exterior components such as dashboards, bumpers, and trim pieces. The process allows for complex shapes and intricate details to be achieved with high precision.
In the healthcare sector, plastic injection molding is utilized for producing medical equipment like syringes, IV connectors, and surgical instruments. The ability to manufacture sterile and durable products makes it an ideal choice for meeting stringent safety standards.
Consumer electronics also benefit from plastic injection molding by creating casings for smartphones, laptops, and other gadgets. The process enables manufacturers to produce lightweight yet durable enclosures that protect delicate electronic components inside.
Eco-Friendly Alternatives to Traditional Plastic Materials
As the world becomes more environmentally conscious, the demand for eco-friendly alternatives to traditional plastic materials is on the rise. Companies are exploring innovative solutions to reduce their carbon footprint and lessen their impact on the planet.
One such alternative gaining popularity is bioplastics, which are made from renewable resources like corn starch or sugarcane. These materials have a similar functionality to traditional plastics but decompose much faster in composting facilities, making them a greener option.
Another promising alternative is recycled plastic. By using post-consumer or post-industrial waste as raw material, companies can reduce dependence on virgin plastics and divert waste from landfills. This circular approach not only conserves natural resources but also helps tackle the global plastic pollution crisis.
Furthermore, some companies are experimenting with plant-based plastics derived from sources like algae or seaweed. These biodegradable materials offer a sustainable option for packaging and products while minimizing environmental harm.
Innovations in eco-friendly alternatives continue to evolve as we strive towards a more sustainable future.